Clean Diesel
What is Clean Diesel?
Current clean diesel technology with improved electronic engine control, fuel injection and emissions control system help to meet emissions limits and delivers high fuel efficiency.
Clean Diesel is a viable option for sustainable transportation in the long term. It combines better fuel economy and higher pulling power than similar-sized gasoline engines and highly effective emissions control technology.
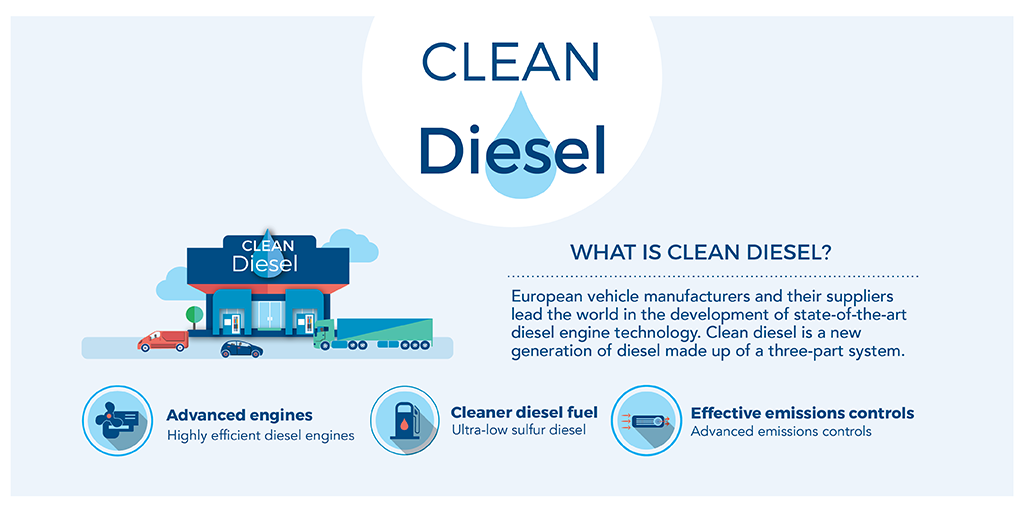
- Today's clean diesel-powered passenger vehicle represents an average of 20 to 25% improvement in fuel economy over similar gasoline powered models.
- The total amount of CO2 emissions of the average clean diesel is 15% less than an equivalent gasoline engine.
- Platinum, palladium and rhodium act as catalysts and are instrumental in significantly reducing emissions. Diesel vehicles are an important means to enable manufacturers to reach the EU's CO2 fleet average targets.
- Further enhanced engine systems in combination with catalyst technology will also enable reduced real driving emissions.
Diesel technology is continuously being improved. Low-emission diesel engines in passenger vehicles, trucks and buses use low-sulphur diesel fuels and specialized catalytic converters, advanced soot filters, and other devices to cut down or eliminate harmful emissions.
Vehicle emissions catalytic converters include exhaust system-related autocatalysts (substrates with incorporated or coated catalytic materials), catalysed particulate filters, and ancillaries such as emissions adsorbers. The latest generation of these products converts up to 99% of combustion engine exhaust pollutants (HC, CO, NOx and particulates), enabled by platinum group metals.
Diesel creates emissions with different compounds compared to a gasoline car. The two primary exhaust elements of a modern diesel are particulate matter (PM or soot), which is essentially unburned fuel, as well as nitrogen oxides (NOx) – including nitric oxide and nitrogen dioxide.
New diesel particulate filters (DPF) can capture from 30% as high as 99.9% of the harmful soot. The PM mass limit at Euro 7 is 4.5 mg/km and with an optimal filter, the number of particles is reduced to levels equivalent to ambient air concentrations.
NOx is a byproduct of air (nitrogen and oxygen) being heated beyond 1,600 Grad Celsius in the cylinder during combustion. To control NOx formation, clean diesel engines today utilize three primary devices: Exhaust Gas Recirculation (EGR), Selective Catalytic Reduction (SCR), and NOx-Adsorber.
EGR works by recirculating a portion of the engine's exhaust gas back to the engine cylinders. This dilutes the oxygen in the incoming air stream and provides gases inert to combustion to act as absorbents of combustion heat to reduce peak in-cylinder temperatures and thereby reduces the NOx production.
Urea-based SCR works by spraying a fluid (AdBlue®) into the exhaust stream to clean up any remaining NOx that EGR was unable to eliminate. The fluid, essentially water and urea, hydrolyses into ammonia and then reacts with the exhaust gas inside the selective catalytic reduction (SCR) to convert NOx into nitrogen and water.
NOx-Adsorbers (NOx traps) work by adsorbing and storing NOx under lean conditions. A typical approach is to speed up the conversion of nitric oxide (NO) to nitrogen dioxide (NO2) using an oxidation catalyst so that NO2 can be rapidly stored as nitrate on alkaline earth oxides. When the storage media reaches its capacity, it must be regenerated. This is accomplished in a NOx regeneration step. In such regeneration, the stored NOx is released by creating a rich atmosphere during very short rich spikes.